Actionable tips to banish bottlenecks from your processes
Bottlenecks can bring production to a standstill. Every manufacturer knows the feeling of encountering a backlog, but manufacturing bottlenecks build up subtly in many cases.
By the time the problem gets your attention, you’ve probably missed an order deadline, blown the budget, or burnt out an employee.
Let’s make sure that doesn’t happen to your business.
What is a bottleneck in a manufacturing process?
Manufacturing bottlenecks are delays in one stage of the production process. They occur when too much work builds up, creating a queue. Downstream processes slow to a crawl until the queue clears.
There are two types of bottlenecks in manufacturing:
1. Short-term Bottlenecks
Temporary snags that will resolve themselves.
For example, a skilled employee goes on holiday or gets sick, your order is stuck in the Suez Canal, or a CNC machine fails unexpectedly.
2. Long-term Bottlenecks
More pernicious bottlenecks that repeatedly frustrate the production process (and your team).
Things like inefficient material transfer processes, manual reporting tasks and double data entry.
How to identify bottlenecks
If you can identify bottlenecks, you’re well on your way to increasing productivity. Short-term bottlenecks are usually obvious, while long-term issues tend to show up when you dig into process data with a strategic approach.
Here are 4 approaches to identifying production bottlenecks:
1. Map Your Processes
Visualise your production process to see where tasks are building up into a backlog. Jobman’s agenda screens will help you identify the exact stage where production slows.
Bonus tip: Take this opportunity to employ value stream mapping, a Lean strategy we discussed in this blog, to turn bottlenecks into boons.
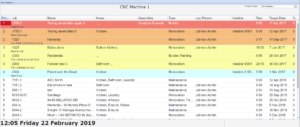
2. Look For Accumulations
In single-line operations, it’s easy to spot the machine or operator with the longest queue. But when you run multiple concurrent lines, identifying the inefficiency requires a more complex analysis – and a good process map (see above).
3. Adjust Throughput
Throughput and bottlenecks are directly related. Increase throughput one machine at a time; the process stage with the biggest impact on output is your bottleneck.
4. The 5 Whys Technique
When you notice an issue, ask, “why is it happening?” Then ask, “why is that happening?”
Repeat the process a few more times – this is the 5 Whys technique.
By the 5th layer down, you should understand what is causing the bottleneck.
How to eliminate bottlenecks
Now, here’s how to eliminate production bottlenecks and unlock productivity:
Avoid Idle Capacity
Keep the bottleneck stage loaded to full capacity. There is a downstream ripple effect; slowing production because of a bottleneck doesn’t solve the issue; it only encourages lower output.
Reduce Strain On The Bottleneck
Make sure your product is in the best possible shape when it reaches the bottleneck stage. Things like inefficient material transfer processes, manual reporting tasks and double data entry.
Manage WIP Limits
Focus on getting one thing done at a time. If you don’t have WIP (work-in-progress) limits in place, set them.
WIP limits prevent your workforce or equipment from receiving too many different tasks at once, leading to inefficient context switching.
Jobman’s capacity planning features make managing WIP limits a breeze.
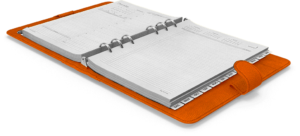
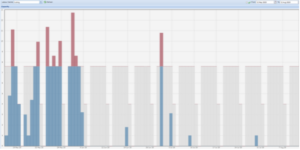
Process Work In Batches
Especially for custom manufacturers, batching similar jobs is another way to avoid context switching.
It might only take a few minutes to recalibrate your equipment for a different type of task, but those minutes quickly add up to hours.
This is where Jobman’s job scheduling tool enables you to quickly shuffle jobs for the most productive outcome.
For example, Jobman allows for different Job types to be viewed on the target calendar. Meaning you could batch jobs that are outsourced for painting to reduce courier expenses.
Curious to know more about eliminating production bottlenecks? Contact the Jobman team for advice on managing your manufacturing business more efficiently with Australia’s leading ERP software.