Accidents happen. Every manufacturer and cabinetmaker is familiar with material defects, missing parts, incorrect assembly and installer damage.
Without an ERP, minor issues are patched over and forgotten. But with Jobman, you can easily keep a detailed record of every issue, reducing re-occurrence and improving productivity.
All the critical data like location, images, descriptions and part numbers remain with the issue alert. So if you need evidence or more information down the track, it’s all there in black and white.
Jobman’s alert management feature reduces waste through error, keeps your team accountable, and provides a safety net against liability claims.
Hear what our clients have to say
Benefits of Jobman’s Alert & Issue Management Software Features
- Critical information is easily accessible
- Submitting alerts is simple for every team member
- Identify recurring defects
- Strategically address recurring issues
- Eliminate bottlenecks
- Automated reminders for overdue alerts
- Submit alerts to superiors in seconds
- See all alerts against individual jobs
- Edit and update alerts in a few clicks
Accountability Made Easy With Alert Management
Making alerts easily accessible eliminates blame and finger-pointing. When a team member submits an alert, Jobman helps fix the issue as efficiently as possible. All the information you need to track and rectify the problem is securely stored in Jobman’s cloud servers, ready for the next person up the chain to review.
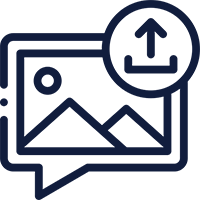
Upload Photos of The Issue
Along with the location, date, type and job details, you can store photos of the issue in the record. This makes it easy to see exactly what went wrong and make a plan to fix the issue.
Any team member can submit multiple photos alongside an issue. They can add comments to each image and submit more photos once a fix is in progress.
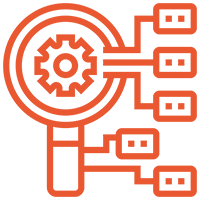
Keep Track of Recurring Issues
It’s often hard to spot a problem that pops up again and again. You have different installers, operators and locations, and often people working in siloed teams. But with Jobman, all your issues appear in the same centralised location. Management can see which mistakes and defects are hurting productivity and then make a plan to address them. You can track all the alerts raised on individual jobs or filter by alert type to spot recurring issues at a glance.
End-to-end operational visibility with Jobman gives you the tools to better plan, track, and manage your manufacturing business.
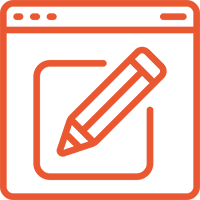
Quickly Review And Edit Alerts
Simply double-click (or double-tap) on the alert to access the details and update its status. Jobman records every change. You can add records to the alert, so your team is fully informed without calling multiple site meetings or sending emails.
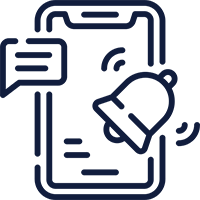
Automatic Next-In-Line Notification
Overdue alerts automatically trigger a reminder to a superior. If that line manager is away, Jobman alerts the next person, so the alert doesn’t go ignored. Admin (usually the managers) set the length of time that an alert can be overdue before a superior receives an automatic notification. This improves accountability and ensures issues get fixed faster.
Intelligently Simple Alerts
Jobman’s alert & issue management feature reduces errors and improves reporting up the line. Alerts is a powerful manufacturing ERP feature by itself. But combined with an extensive suite of productivity and management features providing end-to-end visibility over your business, you’ll wonder how you ever did without Jobman.